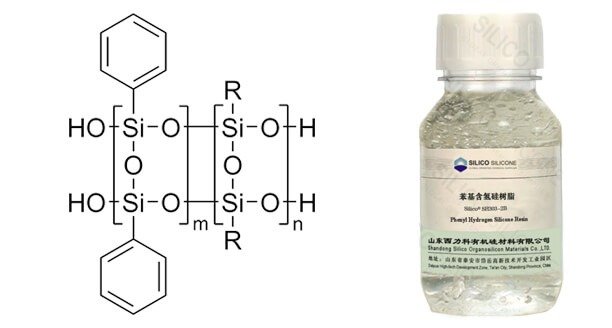
Phenyl Hydrogen Silicone Resin
Silico® Phenyl Hydrogen Silicone Resin is a heat-resistant MQ resin with Si–H bonds and high phenyl content. It offers strong UV resistance, high refractive index, and good bonding with vinyl or hydroxyl silicones.
It’s used in LEDs, optical adhesives, high-temp potting, and insulating varnishes.
Product Overview
Silico® Phenyl Hydrogen Silicone Resin is a high-performance MQ-type silicone resin featuring active Si–H bonds and a high content of phenyl groups. This structure delivers exceptional thermal and UV stability, high refractive index (up to 1.54), and excellent crosslinking performance with vinyl- or hydroxyl-functional silicone systems.
With its superior film-forming ability, transparency, and thermal resistance, Silico® phenyl hydrogen silicone resin is widely used as a crosslinker or modifier in LED encapsulation materials, optical adhesives, high-temperature potting compounds, and insulating varnishes.
Typical Technical Specifications
Property | Typical Value | Remarks |
---|---|---|
Appearance | Colorless to light yellow transparent liquid | Visual inspection |
Hydrogen Content (Si–H) | 0.22–0.52 wt% | Reactive hydrogen for crosslinking |
Viscosity (25 °C) | 40–6,800 mPa·s | Varies by product grade |
Refractive Index (25 °C) | 1.491–1.540 | High optical clarity for LED applications |
Volatile Content (150 °C/3 h) | ≤ 1.0 wt% | Thermogravimetric method |
Solid Content | Typically ≥98% (solvent-free) | 100% active content available |
Key Applications
LED Encapsulation & Optical Materials
As a high-refractive index crosslinker, it ensures brightness, clarity, and UV resistance in silicone-based LED lenses and encapsulants.Electronic Potting & Insulation
Provides excellent dielectric strength, thermal durability, and moisture resistance for motor coils, transformers, and circuit protection.High-Temperature Silicone Rubbers
Serves as a Si–H curing agent for heat-resistant rubbers and RTV/HTV formulations.Hard Coatings & Optical Films
Delivers superior gloss, scratch resistance, and long-term yellowing protection in clear coatings and specialty film layers.
Performance Advantages
Highly Reactive Si–H Groups
Enables fast, efficient curing with vinyl or hydroxyl resins in the presence of platinum catalysts. Ensures controlled crosslink density and final film properties.High Refractive Index (up to 1.54)
Provides optical clarity and brightness in encapsulant and optical film applications.Superior UV and Thermal Resistance
Phenyl modification enhances durability under UV radiation and extreme heat, up to 250 °C+ continuous.Excellent Film-Forming Properties
Forms uniform, transparent, and flexible films with outstanding adhesion and weatherability.Versatile Compatibility
Works with various silicone systems (methyl, phenyl, vinyl-functional resins); excellent dilution and dispersion behavior.
Recommended Grades
Grade | Viscosity (25 °C) | Hydrogen Content | Refractive Index | Recommended Use |
---|---|---|---|---|
Silico® SH303‑2B | 6,500–6,800 mPa·s | 0.22–0.25 wt% | 1.525–1.540 | LED lenses, high-viscosity potting |
Silico® SH303‑2C | 2,700–3,800 mPa·s | 0.22–0.26 wt% | 1.531–1.536 | General electronics encapsulation |
Silico® SH305 | 40–80 mPa·s | 0.46–0.52 wt% | 1.491–1.495 | Coatings, rubbers, low-viscosity blends |
Silico® PH207 | 200–3,000 mPa·s | 0.30–0.50 wt% | 1.49–1.53 | Optical silicones, LED sealing |
Formulation & Curing Guide
Curing Mechanisms:
Compatible with platinum-catalyzed addition curing (Si–H + vinyl), peroxide curing, or moisture-induced systems.Dilution & Blending:
Can be diluted with aromatic solvents or co-formulated with vinyl/phenyl resins for optical clarity and hardness control.Processing Conditions:
Thermal curing recommended at 100–180 °C. Stable under inert atmosphere or ambient air.
Packaging & Storage
Standard Packaging: 25 kg PE drums, 200 kg steel drums, or IBC tanks.
Storage Conditions: Keep in cool, ventilated areas away from acids, alkalis, and metal catalysts.
Shelf Life: 6 to 12 months when properly sealed and stored.
Handling Notes: Avoid moisture and contamination to prevent premature curing or gelation.
Available Documentation
Technical Data Sheet (TDS)
Safety Data Sheet (SDS)
Compatibility & Curing Guidelines
Custom Formulation Support (on request)

Jessica G.
Get in touch to Get
- Quick and helpful reply within 8 hours;
- Tailored solutions provided for your project;
- One-stop purchasing service.